|
ACCESS THE FULL ARTICLE
No SPIE Account? Create one
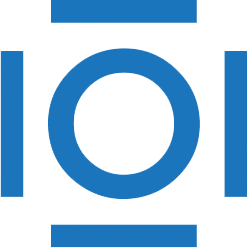
CITATIONS
Cited by 1 scholarly publication.
Sensors
Silicon
Surface micromachining
Microelectromechanical systems
Oxides
Annealing
CMOS sensors