|
ACCESS THE FULL ARTICLE
No SPIE Account? Create one
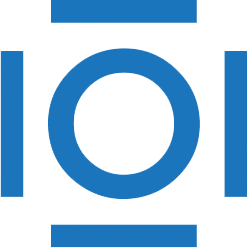
CITATIONS
Cited by 1 scholarly publication.
Control systems
Optical components
Servomechanisms
Analog electronics
Calibration
Computing systems
Data processing