|
ACCESS THE FULL ARTICLE
No SPIE Account? Create one
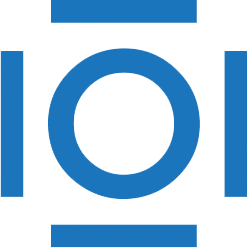
CITATIONS
Cited by 2 scholarly publications.
Manufacturing
Tolerancing
Optical proximity correction
Failure analysis
Design for manufacturability
Capacitance
Clocks