|
ACCESS THE FULL ARTICLE
No SPIE Account? Create one
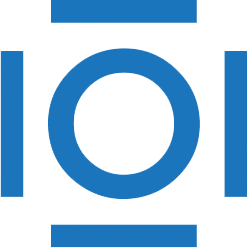
CITATIONS
Cited by 2 scholarly publications and 1 patent.
Silicon carbide
Mirrors
Cryogenics
Distortion
Laser applications
Laser energy
Laser stabilization