|
ACCESS THE FULL ARTICLE
No SPIE Account? Create one
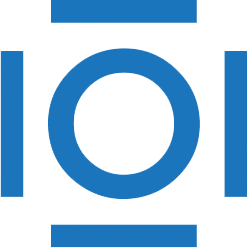
CITATIONS
Cited by 4 scholarly publications.
Standards development
Optical lithography
Scanning electron microscopy
Chemistry
Coating
Current controlled current source
Edge roughness