|
ACCESS THE FULL ARTICLE
No SPIE Account? Create one
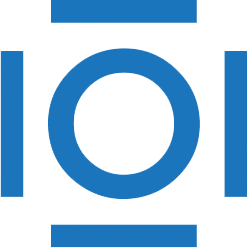
CITATIONS
Cited by 19 scholarly publications.
Reflectivity
Multilayers
Annealing
Extreme ultraviolet
Semiconducting wafers
Mirrors
Silicon